Unveiling the Art of Capital Budgeting in Manufacturing
Embarking on the manufacturing journey demands strategic decisions that dictate the course of growth, sustainability, and profitability. At the nucleus of this strategic maze lies the enigmatic practice of capital budgeting. It’s the roadmap unveiling the path towards optimal resource allocation, the art of investing wisely amidst a myriad of possibilities. For beginners stepping into this realm, navigating through the complexities can be akin to deciphering a cryptic code. Fear not, for this guide unveils the intricate layers of capital budgeting in manufacturing, illuminating each facet to empower you with the insights to make informed decisions and chart a prosperous course for your manufacturing endeavors.
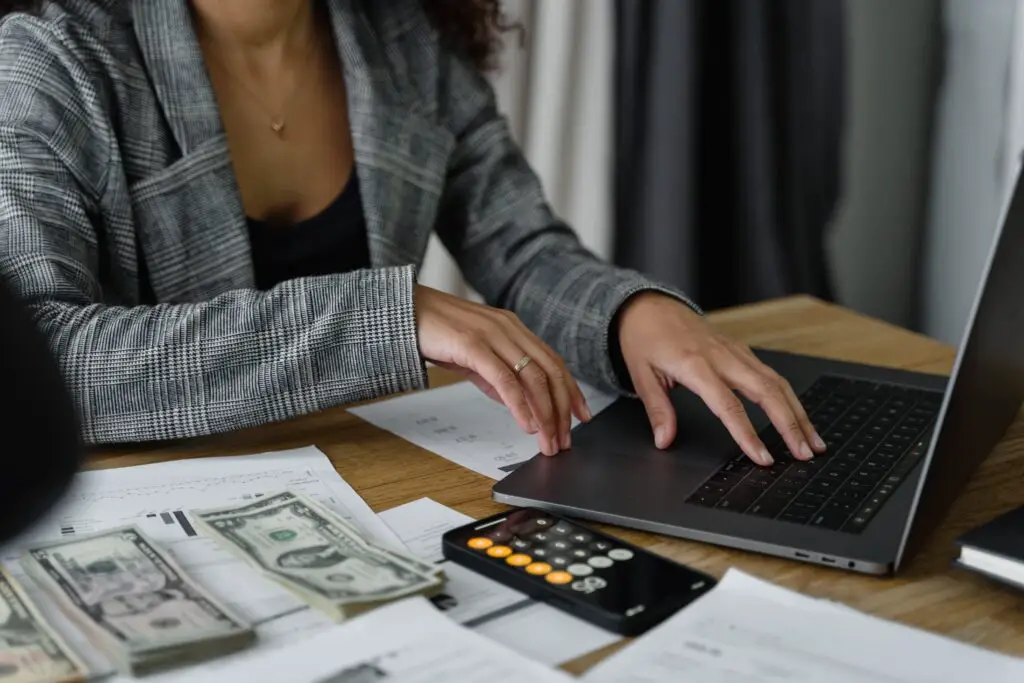
Understanding Capital Budgeting:
Foundation Stones
Capital budgeting lays the groundwork for sound financial decision-making, primarily concerning long-term investments in assets. It’s a meticulous process where potential investments are evaluated, scrutinized, and cherry-picked based on their potential to contribute to the manufacturing entity’s growth. The cornerstone of this practice lies in deciphering which projects warrant the influx of resources, considering their potential returns, risks involved, and alignment with organizational goals. Techniques like Net Present Value (NPV), Internal Rate of Return (IRR), Payback Period, and Profitability Index act as compasses, guiding decision-makers through the labyrinth of investment alternatives. Each method bears its unique strengths and limitations, offering diverse lenses through which to view prospective investments and determine their financial viability.
The Significance of Forecasting and Risk Assessment
Forecasting stands tall as the backbone of capital budgeting. Gazing into the crystal ball of future cash flows and market dynamics enables manufacturers to gauge the potential returns of their investments. This entails analyzing market trends, demand patterns, technological advancements, and economic forecasts to paint an informed picture of the future landscape. Yet, amidst this predictive ballet, lurks the shadow of uncertainty. Risk assessment emerges as the guardian, tasked with identifying, quantifying, and mitigating the diverse risks that hover around investment projects. From market volatility to technological obsolescence, from regulatory changes to unforeseen operational hurdles, every risk demands a vigilant eye and a contingency plan. It’s the art of balancing calculated risks against potential rewards, ensuring that the chosen investments align with the risk appetite and resilience of the manufacturing entity.
Cost of Capital and Funding Dynamics
In the symphony of capital budgeting, the cost of capital plays a leading role, orchestrating the financial equilibrium. Understanding this cost involves dissecting the cost of debt, equity, and retained earnings, harmonizing them into a composite cost that reflects the entity’s borrowing and equity financing strategies. This cost acts as the threshold, dictating the minimum return an investment must yield to be deemed financially prudent. Meanwhile, the funding dynamics juggle the sources from which the capital is procured, balancing between internal funds, debt financing, equity issuance, or even alternative financing models. Each funding avenue bears its own nuances, influencing the entity’s capital structure, risk profile, and overall financial health. Navigating this labyrinth entails a delicate dance, balancing between leveraging external funds to fuel growth and maintaining a sustainable financial structure that ensures long-term stability.
Capital Rationing and Decision Implementation
Amidst a sea of potential investments, constraints often emerge, introducing the concept of capital rationing. This involves allocating limited resources among competing projects, emphasizing the need for astute prioritization. The selection process turns into a strategic game where the chosen projects not only promise profitability but also align harmoniously with the entity’s overarching goals. Once the decisions are made, the implementation phase unfurls, demanding meticulous execution, monitoring, and adaptation. It’s not merely about making the right decisions but also about executing them with precision, tracking their performance, and being agile enough to recalibrate strategies in response to evolving market dynamics.