A safety coordinator is someone who constructs and manages safety systems and policies to reduce risk, minimize harm, and achieve an acceptable level of risk. In this article, we are going to see about Safety coordinator job description.
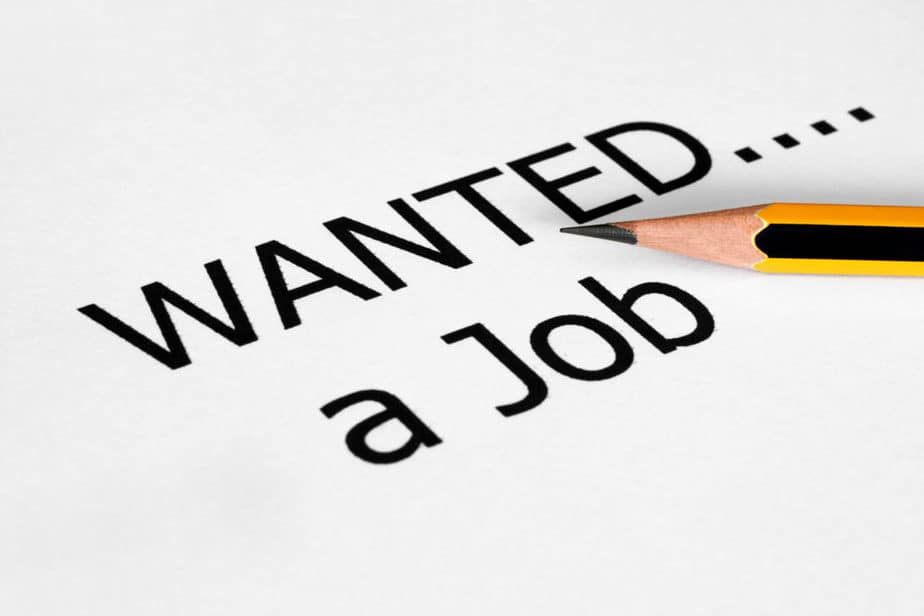
Safety coordinator Job description:
The Safety Coordinator is a member of the safety team at a manufacturing facility. In this role, they will take ownership of all safety training, documentation, and systems development that the Environmental Health & Safety Team requires.
The coordinator will also be involved in project planning and implementation to ensure compliance with applicable regulatory agencies such as OSHA, EPA, etc. Aiding management at both operational and strategic levels.
Essential Job Functions
• Develop and maintain comprehensive safety brief, safety training, PPE, and all other EH&S documents. Review and update after every shift change.
• Maintain a current list of trained employees.
• Safety Document Management: OSHA 300 log, OSHA 3100 log (if required), HAZWOPER registration documents, Formaldehyde Control Plan
• Safety Data Sheets
• Floor marking Safety Zone Map
• PPE check out/check-in system
• Lockout tag out procedures
• Electrical procedure documentation
• Emergency Response procedures (Fire/Medical)
• Chemical inventory forms/systems/procedures for lab chemicals, production chemicals like EHS chemical inventory sheets for each substance.
• HAZWOPER training sign-off sheet
• OSHA injury/illness logs
• OSHA 300 log/300A log (for welders, linemen)
• Injury/illness tracking and review system (SMS, NVS, MULTI-IN)
• Hazardous Communication program- chemical inventory sheets for each substance. MSDS filing system maintained by Safety Coordinator (current with active substances.) MSDS files are maintained by location in a locked file cabinet.
• Chemical Inventory Management – chemical inventory sheets for each location kept in a locked file cabinet.
• Labels and other labeling systems maintained by specialty or production department.
Qualifications required to be a Safety Coordinator:
1. Graduation from high school or equivalent.
2. GED or equivalent if high school did not provide an adequate education.
3. Secondary and college education preferred, (minimum 2 years of college for technical majors).
4. High aptitude for maths, physics, and engineering, patient with manual dexterity, good eyesight, and hearing. The ability to see and hear in many areas at the same time is required to be able to effectively receive clear communication from other personnel in noisy or crowded conditions
5. Must possess a personality that possesses good interpersonal skills to successfully communicate with people from all backgrounds/experiences; must be willing to learn new things quickly
6. Must be at least 21 years of age
Responsibilities:
1. Safety Training and Awareness:
a. Provide safety training to all personnel as required by the EH&S binder and procedures manual.
b. Maintain current training programs for all personnel through annual review of all required training documents periodic refresher training as necessary analysis of results from annual refresher tests to ensure continuous proficiency in the subject material.
c. Provide schedules and training materials to all personnel working in the area being trained.
d. Conduct periodic safety inspections in safety-sensitive areas of the facility to ensure that all personnel are properly trained, have the proper PPE, and are supervised by competent and knowledgeable supervisors.
e. First Aid training: provide to personnel when required via management request or as required by state regulations
f. Provide necessary information relative to emergencies and accidents involving ergonomic concerns, hazardous products or chemicals in process or production areas as a result of having attended OSHA recognized programs for first responders or through attending local conferences relating to HSE/Ergonomic related topics as a safety coordinator
2. Accident Investigation Report:
a. Accident investigation reports are completed at the direction of management as required by occupational safety regulations or as requested by management.
b. Accident investigation procedures are policies and procedures established under OSHA requirements, company guidelines, or departmental policies, which are implemented and followed when an accident is reported to the safety coordinator.
c. Provide records to the following:
1) The fire marshal for his/her records on all permit or complaint fires that occur in this location.
2) The Department of Labor OSHA officer for his/her records on all permit or complaint OSHA inspections that occur in this location.
3) The Department of Workforce Development for his/her records on any occupational injuries, illnesses, or fatalities that occur in this location.
4) The local police department for his/her records on all local crime reports that occur in this location.
3. Hazmat Response Procedures:
a. Follow proper ERG/Hazmat response procedures for spills in the facility.
b. Conduct periodic training with all personnel involved in hazmat situations.
c. Provide all materials required by the fire marshal to permit fires that occur in the facility.
4. OSHA Inspection Procedures:
a. Compliance with OSHA procedures and standards, including those in federal laws, executive orders agency directives, and regulations. Health, safety, and environmental hazards are identified by:
b. Conducting job hazard analysis as required by OSHA and other regulatory agencies as well as recommendations from safety committees or safety-related problems identified by employees or management;
c. Developing written reports for all hazards that are found during the annual or periodic inspections of the plant;
d. Management or employees are made aware of all hazards found, and the corrective actions that are recommended;
e. Providing OSHA with information about the following:
1) The number of employees exposed to hazardous chemicals through their occupation;
2) The number of employees exposed to hazardous chemicals from spills, releases, or other emergencies;
3) The number of hazardous chemicals produced and transported each month;
4) Material safety data sheets for all substances used in the on-site laboratory and production areas.
Attitude and behavior:
1. Safety coordinators must be able to work in a team-oriented environment, as well as independently.
2. Safety coordinators are required to keep up with current safety regulations and be able to actively participate in the development of policies that affect the safety of their workplace.
3. They must also be comfortable making presentations within management.
4. Safety coordinators must be knowledgeable about OSHA standards, and other regulatory agencies ’ standards. This knowledge is necessary so that they can make assessments about potential hazards within their workplace, and create plans for reducing or eliminating those hazards. This may include developing training programs for workers, organizing emergency response procedures and equipment, etc…
5. Safety coordinators must be able to communicate effectively and tactfully.
6. Safety coordinators must be detail-oriented and have good organizational skills. They need to keep up with training records and ensure that workers are properly trained in the necessary procedures.
7. Safety coordinators must be passionate about safety generally, as well as in their workplace in particular.
8. Safety coordinators must know the company’s mission, values, and goals so that they can identify ways in which safety may affect or support those objectives.
9. This position would require travel to attend training seminars or conferences on current regulations, and other related information pertinent to the role of a safety coordinator.
Compensation:
The salary for this position would be determined by the size of the company. A small manufacturing plant would offer a starting salary in the range of $45,000-$60,000.
A large corporation may offer a starting salary upwards of $80,000-$110,000. This would also depend on previous experience and education for the safety coordinator.
How to become a Safety Coordinator?
The role of a safety coordinator is to ensure that employees are trained properly and provided the proper means for performing their jobs safely.
• Complete an online form at www.nyc.gov/dobnow
• Read and complete the following instructions:
a. Application Validation Instructions
b. Safety Coordinator Instructions
• After reading the instructions, you will be directed to fill out a New Appointment Form and bring it to the Division of Appointments for submission
• Once your appointment is submitted, you will have an interview at the Division of Appointments for you to be approved for your appointment by anyone who has been appointed prior or currently holds a Safety Coordinator’s position or anyone that holds the title of Manager. If you are seeking the position because others have retired, transferred, etc., then this meeting is not required.
• Upon your appointment, you will be required to attend a safety coordinator orientation with a current Safety Coordinator at the Center for Safety and Health. During this orientation, you will be provided with a detailed overview of the role of a safety coordinator and OSHA standards.
• You will be required to attend an OSHA-approved trainer on how to conduct an initial hazard assessment in your work area.
• You will be required to attend an OSHA-approved trainer on how to conduct a periodic hazard assessment in your work area.
• You will be required to attend a safety coordinator orientation with the ADA Coordinator. During this orientation, you will be provided with additional information about the ADA Act and how it applies to your workplace.
• You will also receive training from the U.S. Small Business Administration on how to give a successful presentation.
During your annual performance evaluation, you will be required to submit an action plan of the things you want to accomplish within the year. These goals must be reviewed and approved by your supervisor and the ADA Coordinator.
Upon completion of your first year: You will be eligible for another Safety Coordinator Orientation that may include training that is not OSHA-approved as long as they are relevant to the role of a safety coordinator.
Conclusion:
The role of a Safety Coordinator requires the utmost responsibility and commitment. It is important to be knowledgeable about safety regulations relating to your workplace and be able to effectively make presentations and report findings to improve safety protocols. Through this article we would have learnt about Safety coordinator job description.
Below is a list of some books that you can reference to become more knowledgeable in your position so you can better develop plans for reducing, controlling, or eliminating hazards within the workplace.
• Introduction to Incident Investigation. National Safety Council. Chicago, Il.
• Hazards and Accident Prevention, Panjabi, M. S., 6th Ed., McGraw-Hill: New York, NY (2002).
• Industrial Safety Management by Whitehouse, R. W., and Bavington, M. S., 2nd Ed., Cengage Learning: Belmont California (2010).
• Principles and Practices of Hazardous Waste Management by Janet Eisner Granick and Marcia J Goldstein, 3rd Ed., CRC Press: Boca Raton Florida (2012).
• Chemical Accident Prevention Manual by Howard E. Andrews and John F McKean McGraw-Hill Professional Publishing: New York NY (2010).
Some Frequently Asked Questions and Answers:
1. What is the role of a safety coordinator?
The role of a safety coordinator is to ensure that employees are trained properly and provided the proper means for performing their jobs safely.
2. What is needed for you to become qualified for this position?
You must be at least 18 years old; have the U.S. Department of Labor 1099 form.
3. What is OSHA?
Occupational Safety and Health Administration (OSHA). OSHA is the Federal agency responsible for the enforcement of safety and health regulations in the workplace. The Occupational Safety and Health Act of 1970, as amended, (commonly referred to as “OSHA”) empowers the U.S. Secretary of Labor to set standards for a safe workplace, to develop and distribute information on occupational safety and health issues, and to enforce these safety standards.
4. What is the difference between an OSHA-approved trainer and an untrained trainer?
An OSHA-approved trainer has been thoroughly trained in all aspects of safety standards and training.
An untrained trainer does not have the knowledge or skills to conduct proper training on a variety of subjects.
5. What should be discussed in a hazard assessment meeting?
The purpose of this meeting is to examine any hazards that could occur in your work area that may result in an injury. It is recommended that you prepare a list of potential dangers beforehand so they are ready to discuss during the meeting.
6. What actions can you take to prevent hazards within the workplace?
First, it is important to examine each job description for any potential dangers and make a list of them. Then, with other workers, brainstorm solutions.
7. Who should attend?
Anyone who will be working or conducting business in your work area should be allowed to discuss potential hazards that may occur from working in that area. You do not necessarily have to invite all workers, it is up to you to determine who needs to attend.