Unveiling the Essence of Quality Costs:
A Deep Dive into Their Impact on Your Bottom Line
The Essence of Quality Costs
Quality costs, an intricate tapestry woven into the fabric of business operations, encapsulate more than meets the eye. They exist in various forms, often hidden beneath the surface, awaiting discerning eyes to decipher their significance. These costs, comprising prevention, appraisal, internal failure, and external failure expenses, form the crux of a company’s quality management. Prevention costs, the guardians of excellence, encompass measures taken to avert defects before they occur—investments in employee training, robust processes, and sophisticated equipment. Appraisal costs, the sentinels of scrutiny, arise from activities aimed at evaluating and maintaining product or service quality. These encompass inspection, testing, and quality audits that ensure adherence to established standards.
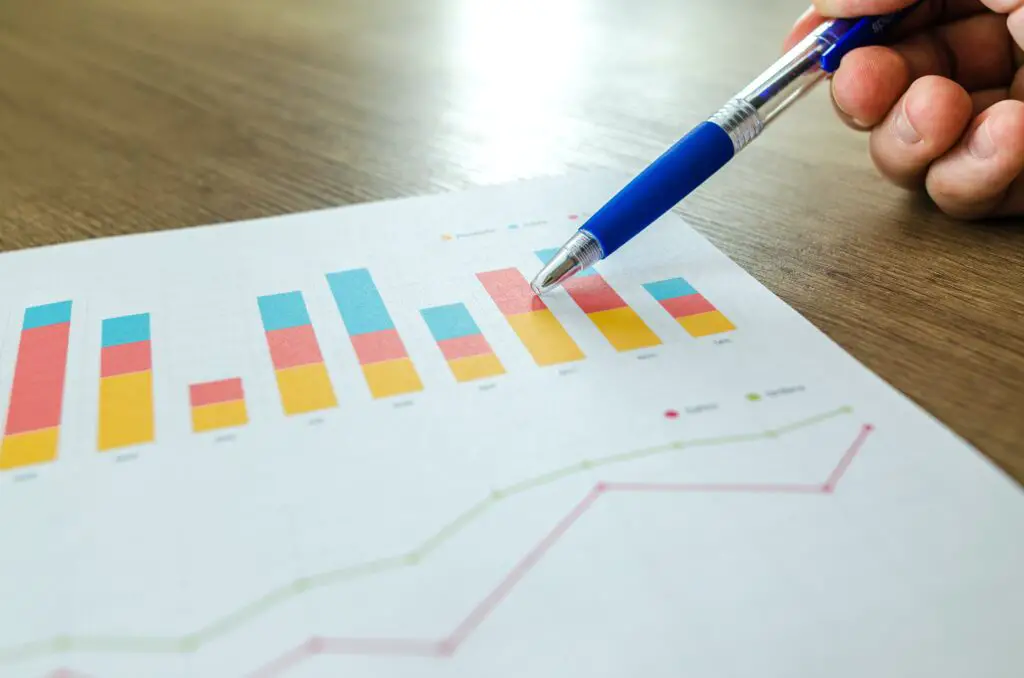
The symbiotic relationship between these costs becomes palpable when considering internal failure expenses. These stem from defects detected within the organization, encompassing scrapped materials, rework, and machine downtime. Akin to a clandestine undercurrent, these costs surface when quality falters within the operational boundaries. External failure costs, the specters haunting beyond the business realm, manifest in customer complaints, product returns, warranty claims, and even legal repercussions. Their impact reverberates far beyond mere monetary considerations, tarnishing brand reputation and eroding consumer trust.
Impact on Operational Efficiency
Quality costs ripple through the operational waters, influencing the tides of efficiency. Prevention costs, akin to fortresses guarding the citadel, act as proactive investments that fortify the foundations of quality. By fostering a culture of excellence and bolstering robust processes, these costs lay the groundwork for sustained operational efficiency. Employees imbued with extensive training and equipped with cutting-edge tools become architects of reliability, sculpting products and services that exude excellence at every turn.
However, the equilibrium pivots when appraisal costs come into play. While essential for maintaining quality standards, an overemphasis on these expenses may inadvertently become shackles, constraining operational agility. The fine line between meticulous evaluation and stifling bureaucracy becomes apparent, impacting the fluidity of processes. The challenge lies in harmonizing meticulous scrutiny without impeding the agile flow of operations, ensuring that the cost of evaluation doesn’t outweigh its benefits.
Impact on Financial Viability
Delving deeper into the labyrinth of quality costs unravels their profound impact on financial viability. Internal failure expenses, like elusive phantoms, lurk within the folds of operations, draining resources and disrupting financial equilibrium. The reworking of defective products, discarding flawed materials, and the downtime incurred in rectifying errors collectively undermine financial robustness. These costs, often stealthily camouflaged within daily operations, chip away at profitability, casting shadows on the bottom line.
The external failure costs, a tempest brewing beyond organizational boundaries, carry repercussions that transcend mere monetary values. They cast an ominous shadow on brand reputation, inciting customer distrust, and marring the perceived value of products or services. The financial toll incurred from addressing customer complaints, processing returns, honoring warranties, and mitigating legal ramifications becomes a testament to the far-reaching impact of quality lapses.
In the Midst of Quality Costs:
A Nexus of Influence on Business Dynamics
Implications on Customer Satisfaction and Loyalty
The ripples of quality costs converge at the nexus of customer satisfaction and loyalty. Prevention costs, the silent architects of excellence, lay the cornerstone for customer delight. Products or services fortified with quality from their inception inherently resonate with consumer expectations. This alignment fosters satisfaction, nurturing the seeds of loyalty as customers find solace in the reliability and consistency of offerings.
However, the delicate equilibrium teeters when internal failure expenses seep into the narrative. Defects or inconsistencies, discovered within the operational sphere, disrupt the idyllic harmony. They become discordant notes in the symphony of customer experience, leading to dissatisfaction and erosion of loyalty. External failure costs, the storm clouds gathering beyond the business horizon, cast a darker hue on customer sentiments. Instances of product recalls, warranties invoked, or legal entanglements tarnish the brand’s perceived trustworthiness, fostering disillusionment among customers.
Strategic Implications for Business Growth
The intricacies of quality costs resonate profoundly in the strategic echelons of business growth. Prevention costs, the vanguards of quality, wield immense strategic potential. Beyond immediate expenses, these investments foster long-term sustainability and competitiveness. They serve as catalysts for innovation, driving continuous improvement and positioning the organization at the vanguard of industry benchmarks.
However, the pernicious undercurrents of internal and external failure costs pose formidable challenges to strategic aspirations. Internal failures act as impediments, impeding progress and diverting resources from growth initiatives. Every penny spent rectifying internal lapses detracts from investments in innovation and expansion. Meanwhile, external failure costs, a harbinger of reputational damage, erect barriers to market penetration and consumer acceptance. The strategic roadmap, fraught with these obstacles, demands a delicate balance between investment in prevention and mitigation of failures.
Unraveling the Tapestry of Quality Costs:
An Ongoing Quest for Balance
Balancing Act: Optimizing Quality Costs
The pursuit of equilibrium amidst quality costs calls for a delicate balancing act. It necessitates an astute understanding of the interplay between prevention, appraisal, internal failure, and external failure expenses. Optimization lies not merely in minimizing costs but in strategically allocating resources where they wield maximum impact. Embracing preventive measures while judiciously leveraging appraisal activities becomes imperative.
This equilibrium transcends mere financial implications, extending to operational efficacy, customer satisfaction, and strategic imperatives. It necessitates a holistic approach where investments in prevention are complemented by agile appraisal, minimizing internal failures and averting the perils of external failures. A symbiotic relationship emerges where each facet of quality costs plays a harmonious role in fortifying the organizational edifice.
Continuous Improvement: The Panacea for Quality Costs
Amidst the labyrinth of quality costs, the beacon of continuous improvement shines bright. It serves as the compass guiding businesses through the turbulent waters of operational exigencies. Embracing a culture of perpetual refinement, wherein processes, products, and services are subject to relentless scrutiny and enhancement, becomes the cornerstone of cost optimization.
Continuous improvement transcends the boundaries of departments, permeating the organizational ethos. It fosters innovation, empowers employees to identify and rectify inefficiencies, and nurtures a mindset that views challenges as opportunities for enhancement. It becomes the fulcrum upon which the optimization of quality costs pivots, steering the organization toward sustained excellence.
In Conclusion
The intricate tapestry of quality costs, woven with threads of prevention, appraisal, internal failure, and external failure, intricately influences the fabric of business operations. Their impact extends beyond financial considerations, resonating across operational efficacy, customer satisfaction, and strategic imperatives. The quest for equilibrium amidst these costs demands a nuanced approach, where optimization and continuous improvement emerge as guiding beacons steering businesses toward sustained excellence.