Origins and Philosophy:
The Birth of a Game-Changer
The Toyota Production System (TPS) didn’t simply emerge from thin air; it germinated from Toyota’s relentless pursuit of excellence. Its genesis dates back to the post-WWII era when resources were scarce, pushing Toyota to rethink traditional manufacturing methods. Rooted in Taiichi Ohno’s visionary insights, TPS was founded on two core principles: ‘Just-in-Time’ (JIT) and ‘Jidoka.’ JIT revolutionized inventory management by minimizing waste and maximizing efficiency, orchestrating a production system where materials arrive precisely when needed. Jidoka, on the other hand, embedded the concept of automation with a human touch, allowing machines to halt automatically when defects were detected, ensuring quality at every step. This fusion of efficiency and quality laid the bedrock for the lean manufacturing model we know today.
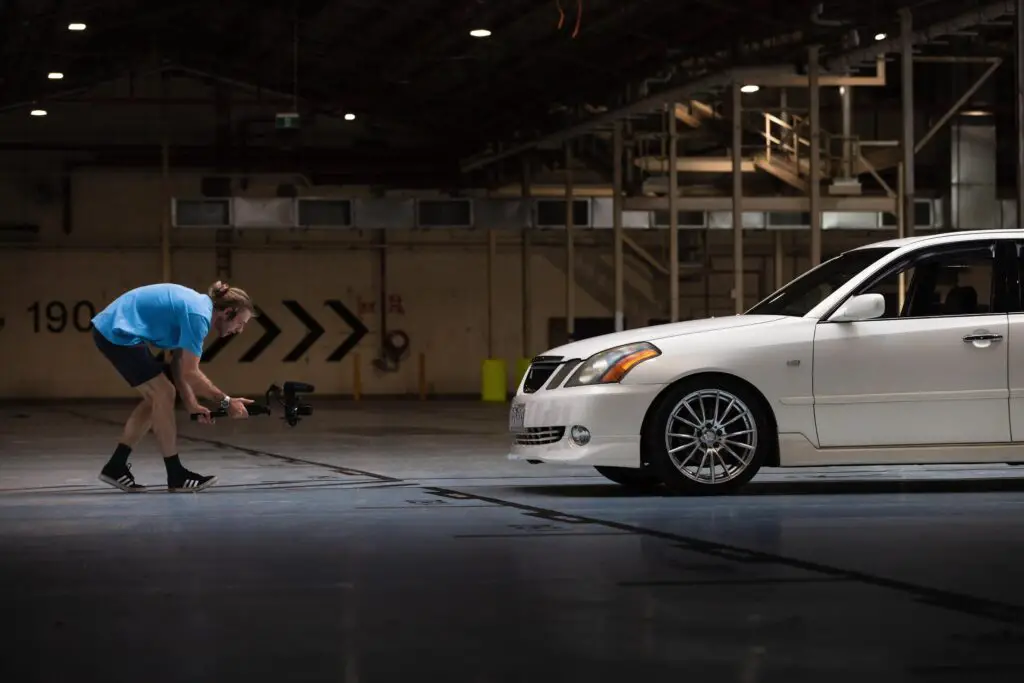
Fundamental Pillars:
The Building Blocks of Lean Excellence
At the heart of the Toyota Production System lie several foundational pillars that uphold its efficiency. One of these is ‘Kaizen,’ the spirit of continuous improvement ingrained into the organizational DNA. It’s not just about grand overhauls but the cumulative effect of incremental enhancements, fostering a culture where every employee is a stakeholder in the pursuit of perfection. ‘Heijunka,’ another vital pillar, emphasizes production leveling, smoothing out fluctuations to maintain a steady workflow. By balancing demand and capacity, this technique reduces waste and amplifies efficiency. ‘Andon’ represents yet another key element, enabling workers to signal anomalies instantly, promoting a culture of transparency and swift problem-solving. These pillars together fortify the system, enabling adaptability and resilience in an ever-evolving manufacturing landscape.
Lean Thinking in Action:
Practical Applications and Techniques
TPS isn’t merely theoretical; its practical applications and techniques wield transformative power in the manufacturing realm. ‘Kanban,’ a visual scheduling system, orchestrates a seamless flow of materials through the production process. It’s a visual cue that regulates inventory levels, aligning with the JIT principle and optimizing resource utilization. ‘Poka-yoke,’ an ingenious concept, involves designing foolproof systems to prevent errors or defects. Whether through simple mechanisms or sophisticated technology, this approach minimizes human error, enhancing product quality. ‘Value Stream Mapping’ acts as a guiding compass, dissecting the entire production process, identifying wasteful steps, and streamlining operations for maximum efficiency. These techniques, when wielded adeptly, pave the way for a leaner, more responsive manufacturing ecosystem.
Beyond Manufacturing:
TPS Principles in Diverse Sectors
The impact of the Toyota Production System transcends the manufacturing domain, permeating diverse sectors worldwide. Healthcare, for instance, has embraced TPS principles to enhance patient care and streamline hospital workflows. The application of JIT principles in healthcare logistics ensures that medical supplies are available precisely when needed, optimizing resource utilization and reducing costs. Similarly, the service industry has harnessed TPS methodologies to refine processes, improve customer experiences, and bolster operational efficiency. From banking to education, the principles of lean thinking have proven adaptable and effective, reshaping operational paradigms across sectors.
Challenges and Evolution:
Adapting TPS in a Changing Landscape
Despite its revolutionary impact, implementing the Toyota Production System isn’t without its challenges. Cultural shifts within organizations, resistance to change, and the need for a comprehensive understanding pose hurdles in the adoption of lean methodologies. Moreover, in today’s tech-driven world, Industry 4.0 introduces new complexities and opportunities. As manufacturing evolves, integrating TPS with emerging technologies like AI, IoT, and robotics becomes imperative. The evolution of TPS entails a harmonious blend of tradition and innovation, navigating these challenges to stay relevant and continue revolutionizing the manufacturing landscape.
The Toyota Production System isn’t just a manufacturing philosophy; it’s an ideology that champions efficiency, quality, and continuous improvement. Its legacy reverberates across industries, reshaping conventional practices and propelling organizations toward excellence. As we delve deeper into the intricacies of TPS, it becomes apparent that its principles, applications, and evolution resonate far beyond the assembly line, embodying a timeless ethos of optimization and adaptability.