Unraveling the Tapestry of Eight Manufacturing Wastes:
A Comprehensive Exploration
Within the intricate tapestry of manufacturing, the concept of waste looms large, casting shadows on efficiency and productivity. The quest to minimize waste is akin to an artist perfecting every stroke, seeking harmony and precision in the canvas of production. At the core lie the eight manufacturing wastes, concealed adversaries that plague industries worldwide. From the subtle nuances of overproduction to the lurking shadows of defects, each waste presents a distinct challenge, demanding astute understanding and innovative solutions. In this journey through the labyrinth of manufacturing, we shall delve into the depths of these wastes—unraveling their definitions, exploring their origins, and illuminating pathways toward their eradication.
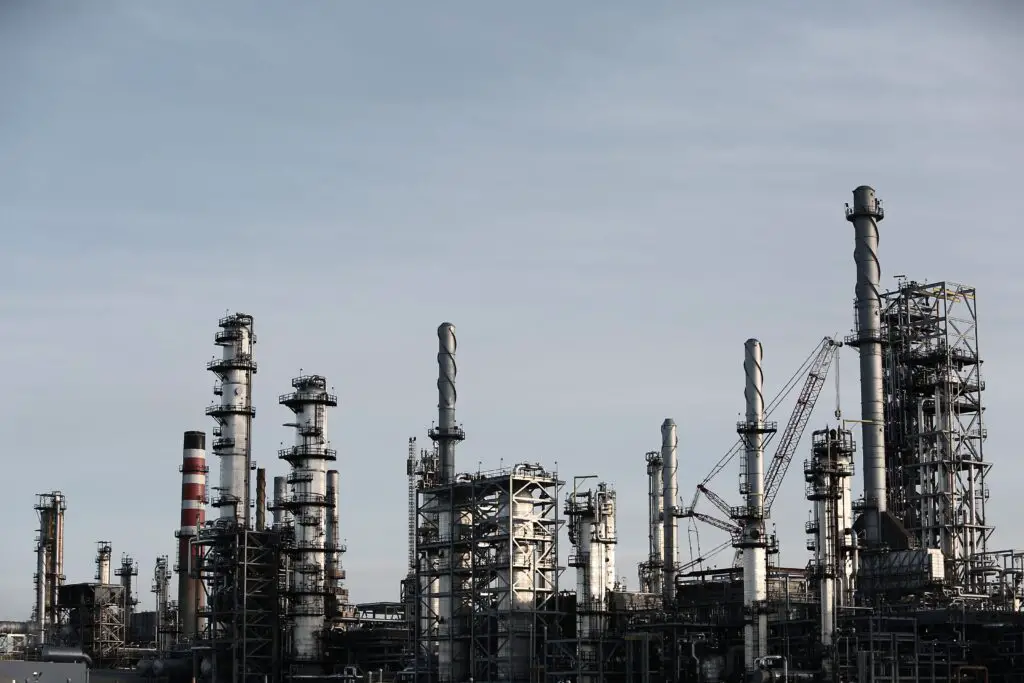
Overproduction:
In the symphony of manufacturing, overproduction orchestrates discord. It is the surplus, the excess, the unnecessary crescendo that disrupts the rhythm of efficiency. Rooted in the desire to meet imagined demands or driven by misguided forecasts, overproduction floods the floor with goods beyond immediate necessity. The causes stem from a lack of synchronized processes, a misunderstanding of market demands, and the relentless pursuit of high-volume output. Solutions unfurl through the meticulous threading of Just-In-Time (JIT) systems, harmonizing production with demand, optimizing inventory, and recalibrating processes to respond nimbly to market fluctuations.
Inventory:
A silent burden, inventory stands as a tangible testament to unmet needs or miscalculated projections. Excessive stockpiling suffocates cash flow, occupies precious space, and camouflages inefficiencies within the manufacturing process. The root causes often intertwine with overproduction, misaligned supply chains, and inadequate forecasting methodologies. Solutions untangle this conundrum through agile inventory management systems, adopting lean principles, and fostering seamless communication between production and demand signals. The art lies in finding the delicate balance between supply and demand, where inventory becomes an asset rather than a liability.
Waiting:
The haunting interlude in the manufacturing symphony, waiting manifests as idle machines, dormant workforce, and paused processes. Its origins lie in the shadows of inefficiency, stemming from disjointed workflows, machine downtimes, and erratic scheduling. Solutions breathe life into these stagnant moments by optimizing processes, synchronizing workflows, implementing preventive maintenance schedules, and orchestrating efficient resource allocation. Time, once lost to waiting, becomes a canvas for increased productivity and streamlined operations.
Transportation:
In the dance of manufacturing, transportation waltzes as a silent, often overlooked, adversary. The unnecessary movement of goods from one point to another orchestrates a cacophony of inefficiencies. Rooted in disjointed layouts, inefficient logistics, and excessive handling, transportation waste hinders the seamless flow of production. Solutions unfurl through layout optimization, strategic placement, streamlined logistics, and embracing technologies that minimize unnecessary movement while maximizing efficiency.
Motion:
The ballet of motion within manufacturing often falls prey to unnecessary and excessive movement. From workers reaching out for tools to inefficient layouts that necessitate extra steps, motion waste stealthily chips away at productivity. The causes intertwine with poor workplace ergonomics, disorganized workspaces, and suboptimal layouts. Solutions intertwine the human touch with ergonomic designs, streamlined layouts, and the strategic placement of tools and resources within easy reach, thereby choreographing a symphony of streamlined motion.
Defects:
The elusive specter haunting manufacturing floors, defects mar the perfection sought in every product. They emerge from the shadows of substandard processes, inadequate training, and compromised quality control. Solutions weave a tapestry of quality-centric cultures, robust quality control systems, continuous training programs, and feedback loops that transform defects into catalysts for improvement rather than detriments to progress.
Overprocessing:
A silent thief of resources, overprocessing embellishes products beyond the desired threshold, consuming time, effort, and materials. It arises from unclear specifications, redundant steps, and excessive quality checks. Solutions unravel through streamlined processes, meticulous specification clarity, value-stream mapping, and eliminating non-value-added activities, allowing the refinement of products without unnecessary embellishments.
Underutilized Talent:
In the mosaic of manufacturing, underutilized talent stands as a stark paradox—skilled individuals restrained from contributing their full potential. It emanates from hierarchical constraints, lack of empowerment, and insufficient engagement. Solutions empower individuals, fostering a culture of innovation, embracing cross-functional collaboration, and decentralizing decision-making to harness the diverse talents within the workforce.
Within the intricate tapestry of manufacturing, these eight wastes entwine themselves, complicating the pursuit of efficiency and perfection. Yet, through astute understanding, strategic interventions, and a relentless pursuit of improvement, industries transcend these challenges, weaving a new narrative of streamlined processes, enhanced productivity, and unbridled innovation.